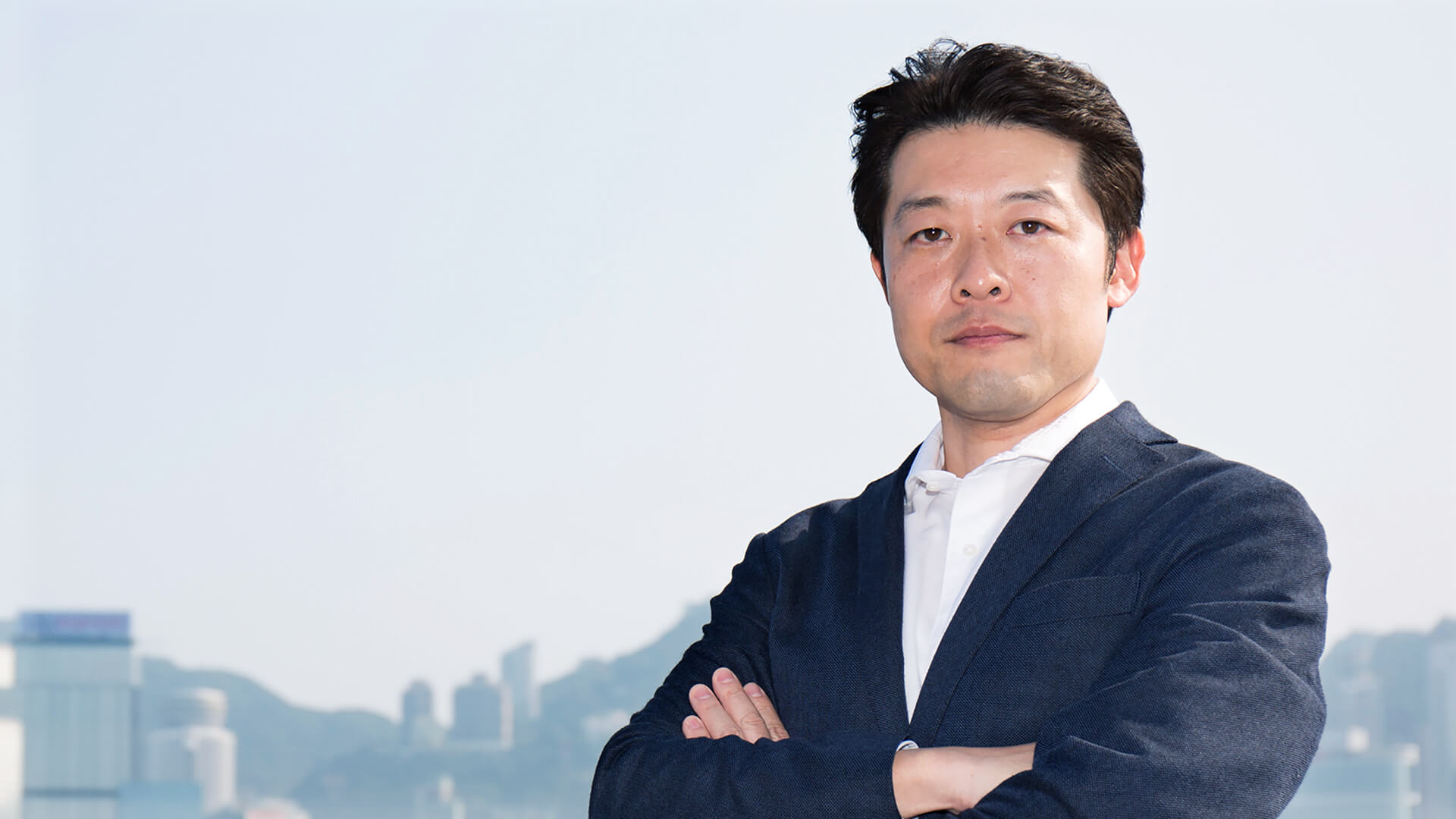
People
渡邉 貴彦
Mitsui Bussan Frontier (China) Co., Ltd.出向
董事副総経理
在香港
ICTの普及と共に裾野を広げ、年10%以上の成長が続く先端材料市場。多彩な情報の表示媒体として、その中でもキーデバイスとなっている液晶モジュールのEMS(Electronic Manufacturing Service)事業を、今日も渡邉貴彦は支えている。
「先端材料」を支える「泥臭さ」
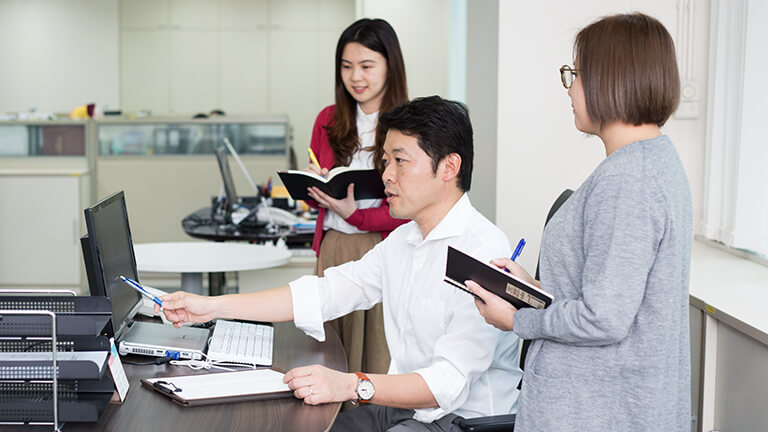
いま私が手がけているのは、スマートフォンや車載用ディスプレイの液晶モジュールの製造受委託事業です。「液晶モジュール」とは、スマートフォンでいうと、画像を映し出すディスプレイとタッチパネル機能を含めた製品の顔の部分。その組立業務を液晶メーカーから受託、中国のパートナー企業とともに生産にあたっています。中国広東省の東莞市にある工場では、1日約15万台、実に1秒に1.5台のスマートフォン用液晶を組み立てている計算です。
東京に18名、香港・東莞に24名というチームであたっており、私はMBFC社の副社長を務めています。営業GMを兼務し、営業関係のすべてを統括する立場です。東京側と連携した事業設計や設備投資から、日々の運営・トラブル対応、パートナー企業とのコミュニケーションまですべて見ています。オフィスは香港ですが、週の半分は東莞の工場にいる感じですね。
この仕事で大変なのは、いろんなことの「予測がつかない」こと。想定外のトラブルが起こるんです。倉庫のエレベーターが止まって物が下ろせないとか、保冷部材を入れておく冷蔵庫の電気が止まったとか(笑)。想定外ということは対応がマニュアル化できないということですから。臨機応変でスピーディーに判断する必要があります。
絶対に避けなければならないのは、生産ラインが止まること。そのためには、常に先を読んでトラブルを未然に防ぐことがもちろん第一。けれど、それでもトラブルは必ず起きます。その時に、いかに生産への影響をミニマイズするか。その判断力と行動力が求められています。
一方、この仕事でいちばんやりがいを感じるのもまた問題を乗り越えた時です。特に印象に残っているのは、2015年にそれまでの商売のスキームの変更を余儀なくされた時のこと。従来のやり方では年間20億円規模のコスト増となり、翌年以降の事業の存続が危ぶまれる事態に直面しました。これをなんとか回避すべく、私たちは、東莞市での実績がないことから断念してきた、一段階進んだ保税加工ライセンスの取得に挑みました。それまでの商売の土台をゼロから作り変える作業となりましたが、約1年がかりで中国のパートナー企業と一丸となって取り組んだ結果、何とか期限内に取得。ビジネスの継続にこぎつけました。
私の仕事の領域は、「先端材料」と呼ばれる分野です。しかし、その先端性は、実は「泥臭さ」で支えられています。スマートに仕事しようとするだけでは決して生まれない。現場で問題を一つ一つつぶし、多様な経験を次なる解決力や予見力として蓄積していくことではじめて実現できるものがある。そう考えています。
お客様の期待を超える使命
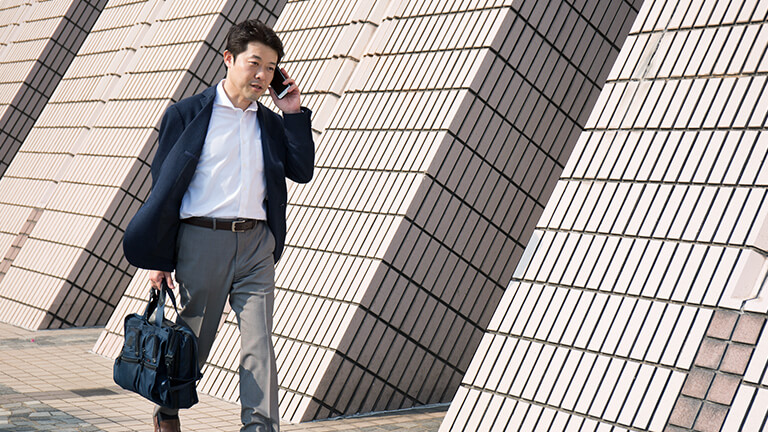
私は、20代の頃は電子材料の“モノ売り”を担当していました。韓国の基板メーカーが主なお客様。毎週のように出張し、まだ知られていない素材を採用していただくために営業していました。そのモノ売りの感覚からすると、製造の受託という仕事はある意味特殊です。お客様から「これがほしい」という素材のレシピを無条件でいただけるわけですから。
モノ売りで成果を上げるには、お客様が何を求めているか常に想像し、考え抜き、提案する必要があります。お客様の求めるものを見抜く力が仕事の品質を高める根幹だったのに、今はそれを明示していただけることが前提。そのことを当たり前と思うようになりたくないな、という感覚があります。ラクをしているような気になってしまうんですね。
ニーズに対する感度を研ぎ澄まし、それに応えたい、それを上回りたい、と工夫すること。それが付加価値の源泉。お客様のレシピをただ実現するのではなく、それ以上の満足をお客様に提供したい。それが三井物産の使命であり、そうすることで信頼感が生まれ、それが次の仕事につながる。いつもそう思っています。
責任感の集合体が品質を上げる
EMS事業を成功させるキーワード。それは「融合」ではないかと思います。コーディネーションやコラボレーションというレベルを超える機能融合。そしてさまざまな立場にある、さまざまな人材のプロフェッショナリズムの融合です。
東京側、香港側、東莞側、私たちの事業には数多くの人が関わっています。そこでは立場も境遇も大きく異なり、本当の意味でお互いに共感できるかといえば難しいかもしれない。けれど、共感しあうことが難しいと一人ひとりが自覚できた時にこそ、全体の中で「自分にしかできない役割」の意味を肚落ちさせることができる。
今日自分がここでこれをやらないと、工場であの仕事をやる人が困ることになるな。東京であの仕事が行き詰まってしまうな。やっといてあげなきゃ。そういう意識を各々が持つ。いわば、みんながひとつの仕事をしているということへの「責任感の集合体」。それが仕事の品質を上げていく。私はそういう発想でマネジメントしています。
先日、大手自動車メーカーOBで品質管理部長をされた方に、スマートフォンのように短期で大量生産を求められる製品の品質管理手法について伺う機会がありました。その方は、私たちがトライしているようなモデル、つまり「半年から1年という短い開発期間で、製品品質と経済合理性を両立させ、かつ大量の製品を供給することを、サプライチェーン全体で最適化する」ようなマネジメントモデルは、自分の知る限りまだないとおっしゃっていました。私たちのビジネスで知見をためていけば、10年後くらいにMBAの科目になっているかもしれないよ、と(笑)。
MBAの科目は話半分としても、それを伺ってがぜん燃えてきました。当社のように無数のビジネス現場を知る会社だからこそつくれる、コンシューマーエレクトロニクスの大量生産に適した管理モデルがあるはずだ。私はいま、そんなことを考えています。
2018年6月掲載