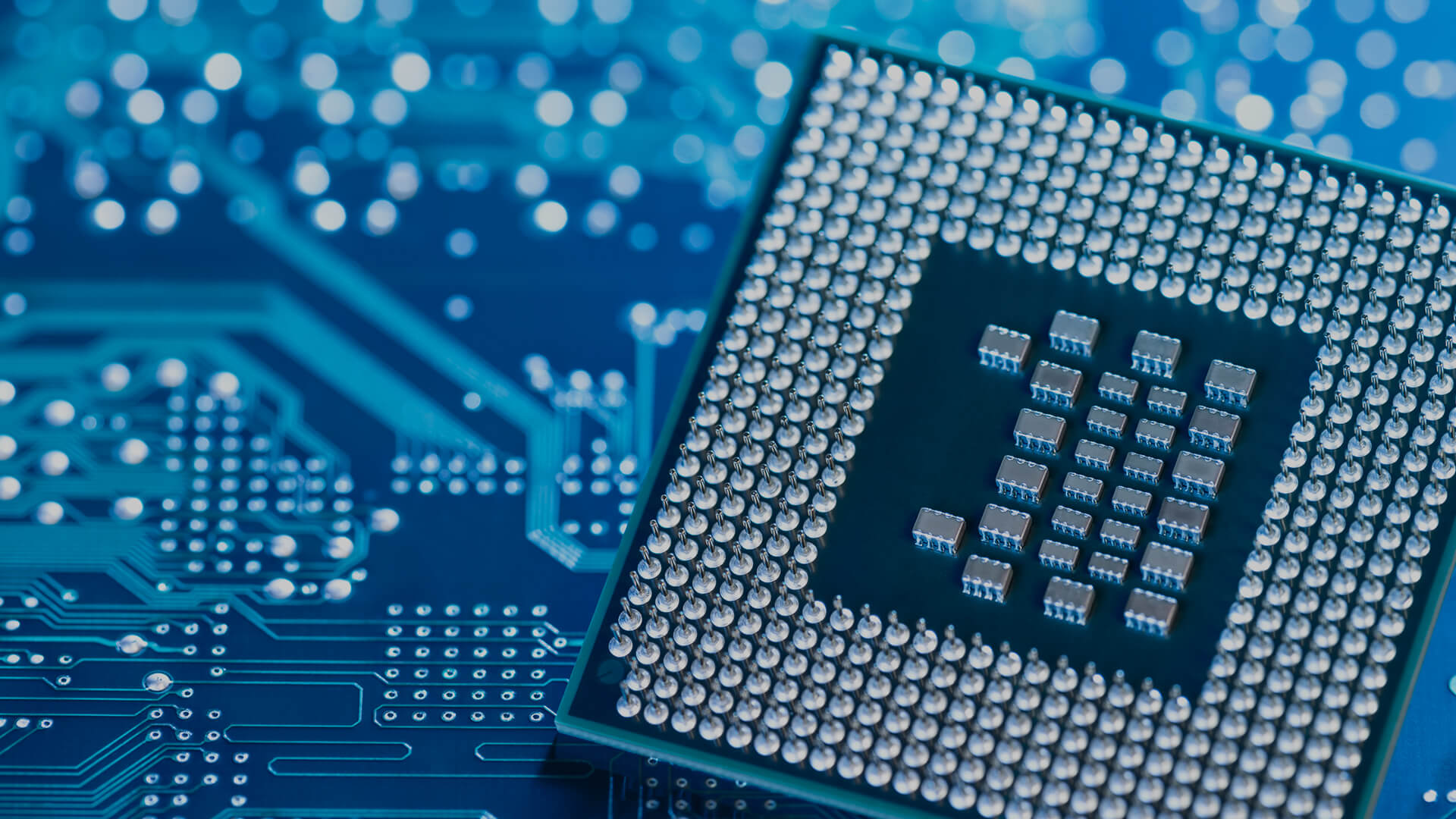
Business Innovation
Fabless is More:
Streamlining global smartphone production
The consumer electronics products that we take for granted are made by a chain of contract manufacturers working together. Mitsui is part of that chain, fine-tuning the manufacture of display modules for high-end smartphones.
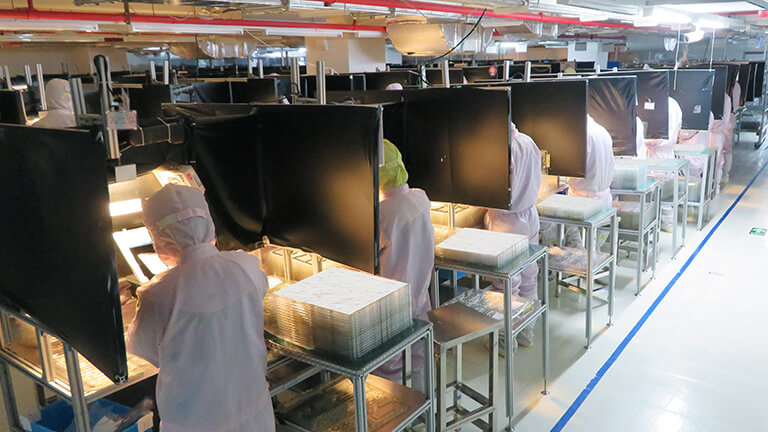
In the 1980s, the semiconductor introductory jettisoned the old vertically integrated production model. Rather than designing and manufacturing chips in-house, US companies started outsourcing their manufacturing to semiconductor foundries in Asia. This model came to be known as “fabless” because third parties handle the “fabrication” side of things.
The fabless model has now taken firm root in the consumer electronics sector. The assembly of personal computers, tablets and smartphones for big-name brands is handled by EMS (electronics manufacturing services) providers, some of which are enormous companies in their own right.
But the big EMS providers do not manufacture devices from scratch; instead, they produce the finished products by assembling a number of prefabricated modules. In the case of smartphones, these include the LCD module (for display and touch) and the battery module (for power). Making the modules is the responsibility of manufacturers with expertise in the relevant technologies. They often subcontract the actual business of assembly to third-party manufacturers in China, Korea and Taiwan.
This has spawned a complex and dynamic supply chain. A comparison of the automobile and smartphone industries gives an idea of its sheer scale and speed. Every year 100 million cars and trucks are manufactured; for smartphones, the figure is 1.8 billion. Car models change every five years; for smartphones it’s something between six months and a year, with design lead times compressed in proportion.
Moreover, even as smartphones get thinner, lighter, and more energy-efficient, prices trend relentlessly downward. Despite its volatility and difficulty, the market is growing. According to the Fuji Chimera Research Institute, the market for electronics components expanded just under 60 percent between 2011 and 2016, for an annual growth rate of over 10 per cent.
In other words, healthy profits can made at the module-assembling end of the supply chain—provided you can produce high-quality products in large volumes at high speed at a competitive cost and on a just-in-time basis! With such a high bar, good technology alone is not enough. Manufacturers need a business model that enables them to successfully overcome all the inherent logistical challenges.
The role of an organizer
This is where “organizers” or “solution providers” come in. Organizers partner with manufacturers to help them develop perfectly streamlined end-to-end processes. This is precisely what Mitsui is doing with LCD modules for smartphones. A team of around 50 people in Mitsui’s Advanced Materials Division acts as organizer for a Chinese manufacturer that assembles 50 million LCD modules for high-end smartphones every year.
An annual output of 50 million modules translates to one million units per week, 150,000 units per day, or 1.5 units per second—for 24 hours a day, 365 days a year. The quantities are staggering. Every month, our partner’s Chinese factory takes delivery of 130 truckloads of materials and components. These are assembled into LCD modules by 5,000 people working on 20 or so production lines and shipped out at the rate of 100 truckloads per month. Since our partner produces 40 varieties of LCD module, each containing around 30 components, the inventory Mitsui has to manage consists of some 1,200 different components.
For such a complex process to function flawlessly at speed, perfect planning and execution are essential. As the organizer, Mitsui has four key responsibilities. These are to (i) control inventory, (ii) organize the delivery of components/materials, (iii) set up, manage and optimize the production process, and (iv) deliver the finished and quality-checked modules to the customer on time.
A full fusion of functions
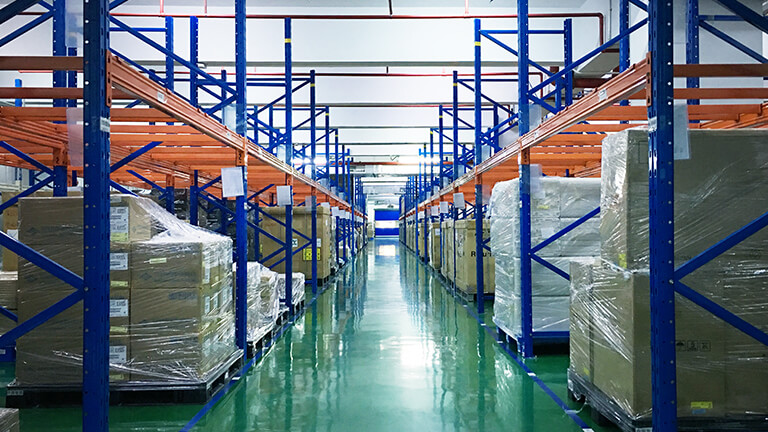
Mitsui, however, has a number of additional strengths it can bring to the organizer role. First, because the Advanced Materials Division of Mitsui has been performing this role for over 15 years, it has built up the know-how to quickly locate and remedy any defects in the process, meaning it can manufacture products according to the customer’s “recipe” with no cost overruns. Second, as part of a large, well-capitalized company, Mitsui can provide financing. Mitsui purchases huge volumes of inventory on behalf of our Chinese partner every month, sparing them heavy upfront costs. We also purchase the production equipment, for which our partner pays us back over a mutually convenient period, again reducing their financial burden. Third, we have an extensive network of relationships with key suppliers. (Many of the key materials in LCD modules are actually made by Japanese companies.)
All this means that Mitsui is far more than a mere coordinator. Leveraging our know-how in logistics and production, we can bring down costs dramatically. Meanwhile, with our in-depth knowledge of materials and processes, we can propose ideas for next-generation products to our Chinese partner. Finally, thanks to the bird’s-eye view we have of the whole value chain, especially downstream, we can help our suppliers realize the full potential of the materials they make.
Consumer electronics manufacturing is a hyper-competitive field. Few contract manufacturers last the course. The fact that Mitsui has been producing modules for the same customer for more than 15 years is testimony to our resilience and our ability to implement continuous improvements in processes and technology. As digital technology becomes ever more all-pervasive in our lives—with digital displays in automobiles, for example—we expect this field to continue to grow. Together with our Chinese partner we will keep producing the electronics products the world needs with unbeatable speed and quality.
Posted in June 2018