Mitsui & Co. Global Strategic Studies Institute
Development of Automotive Steel Supply System in Mexico
Oct. 5, 2016
Masaru Ohnishi
Industrial Studies Dept. I
Mitsui Global Strategic Studies Institute
Main Contents
Expanding Automobile Production Capacity in Mexico
With the growth of the US automotive market, foreign automakers (finished-car manufacturers) have been aggressively expanding their production capacity in Mexico. Mexico’s share of North American production (in Canada, the US, and Mexico), although under 10% up to and through the 1990s, surpassed 20% (approximately 3.4 million units) in 2015. Since Volkswagen (VW) and Nissan started full operations in Mexico in the 1960s, there have been two to three new investment projects in each decade, which has added 500,000 to 900,000 units of production capacity there. In the US, production capacity was reduced substantially due to financial crises in the late 2000s. Thereafter, as the market went into a rapid expansion on the way to economic recovery, auto plants were in nearly full operation, running at over 90% of capacity. In response, Nissan made a new investment in 2013 in Mexico, followed by other automakers, which resumed the expansion of production capacity. The Mexican Automotive Industry Association expects that automobile production capacity and output in Mexico will reach 5.6 million units and 5.3 million units, respectively, by 2020. There figures are about 1.6 times the 2015 levels. Automakers’ increasing production capacity in Mexico also brought primary suppliers for automakers to the country; primary suppliers’ production sites in Mexico totaled more than 500 as of 2014. However, it has been pointed out that secondary and subsequent suppliers and material manufacturers are lagging in this regard. This report focuses on the supply structure for automotive steel in Mexico and discusses how Japanese companies have advanced into the markets.
Issues and Risks Associated with Entry into Mexico
Slow moves into the Mexican market by secondary and subsequent suppliers and material manufacturers are shown in the World Economic Forum’s Global Competitiveness Index (GCI), which ranks Mexico 36th in value chains, far behind Japan (first) and the US (seventh) (see Fig. 1). This is partly because the basic materials industry, which provides raw materials for automobile production, is capital-intensive; thus, cheap labor—Mexico’s advantage—is not necessarily an important factor. In addition, Mexico’s slow infrastructure development has made land transport cost higher, which is another barrier to new entrants into the country. According to consulting firm KPMG, international transport cost in Mexico is 2.7 times higher than in Japan, and 1.4 times higher than in the US, largely due to expensive land transport. For steel, transport by land from the US costs more than by sea from Japan by several tens of dollars per ton.
In addition, the risks of moving into the Mexican market have been heightened by Mexico’s small domestic new car market and high dependence on exports to the US. Currently, 80 percent of automobiles produced in Mexico are shipped as exports, over 70 percent of which are destined for the US. Moreover, South America (i.e., the four member states of Mercosur) was a promising destination, as Mercosur and Mexico concluded an agreement to cut auto tariffs in 2003, but no great expansion has been witnessed so far. Brazil, a major market in South America, has seen sluggish auto sales due to not only its slow economy, but also agreement amendments, which set the tariff-free export ceiling. Meanwhile, Mexico’s domestic market remained limited by used cars flowing in from the US. In Mexico, despite its introduction of restrictions on used car imports in 2013, almost 40 percent of auto sales, combined with unofficial sales, stemmed from used cars. As a result, the US’s demand trend alone can have a tremendous impact on automobile production in Mexico.
Developing Auto Steel Supply System in Mexico
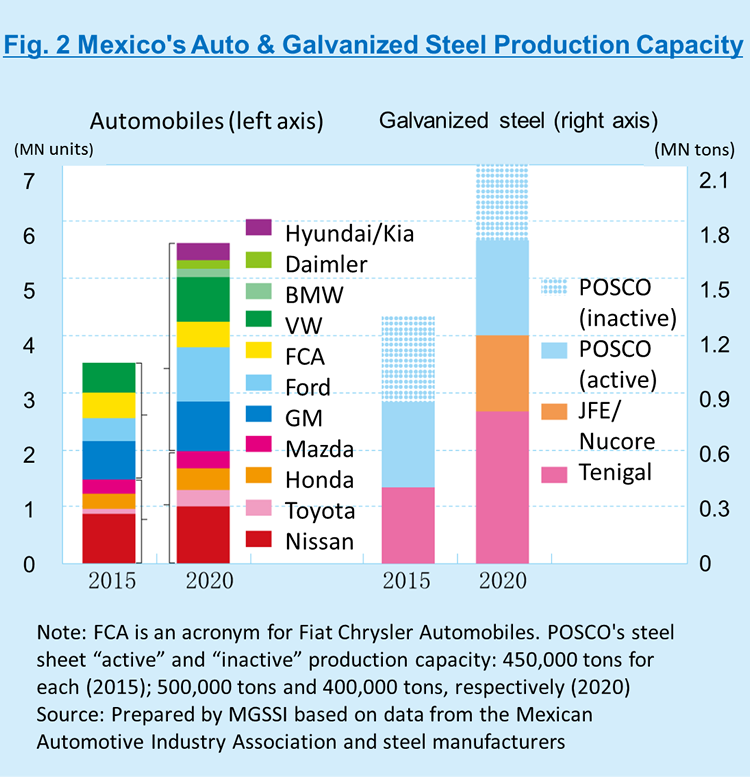
Despite these issues and risks, steel manufacturers are expanding their capacity to supply automotive steel sheets in Mexico. The country’s automobile production capacity is expected to reach 5.6 million units in 2020, 40% (2.27 million units) of which are from US-affiliated automakers (including FCA), 35% (1.97 million units) from Japanese firms, 19% (1.08 million units) from European firms, and 5% (0.3 million units) from Korean firms (Fig. 2). Japanese automakers, which hold the second largest share after their US counterparts, are moving to increase production capacity by 500,000 units from the 2015 level. This trend is driving their main suppliers—Japanese steel manufacturers—to build new lines at their local sites.
To produce hot-dip galvanized steel sheets mainly used in automotive manufacturing, Tenigal, a joint venture between Nippon Steel & Sumitomo Metal and South American steel leader Ternium, owns one line (400,000 tons), while South Korean POSCO has two lines (totaling 900,000 tons). Nippon Steel & Sumitomo Metal and ArcelorMittal operate a joint venture plant in Calvert, Alabama, which can produce 1.4 million tons, part of which is exported to Mexico. In addition, more production lines will be installed in 2019. Tenigal is geared to add a production line (400,000 tons), and a joint venture between JFE and Nucor, a US electric furnace manufacturer, plans to introduce a new production line (400,000 tons). When these two lines are put into operation, the production capacity of galvanized steel sheets in Mexico will total 2.1 million tons. It is estimated that the average car weighing over one ton uses 300 kilograms of galvanized steel sheets. In 2020, even if Mexico’s automobile output should be in line with the AMIA’s forecast (5.3 million units), total demand for steel sheets would be more or less 1.6 million tons, which means an oversupply of some 0.5 million tons. POSCO, accused of dumping steel base material imports from its home country, has voluntarily restricted its supply in an effort to avoid possible trade issues, and it currently operates at half-capacity. If the Korean steel producer continues to operate at this level, it will not necessarily run into the situation that supply exceeds demand, but the fact remains that the country holds an excess capacity of one whole production line. With respect to Japanese automakers alone, the total production capacity in 2020 is almost two million units, and their corresponding demand for galvanized steel sheets is calculated at approximately 0.6 million tons. Japanese steel manufacturers (Tenigal, JFE/Nucor) alone have a supply capacity of 1.2 million tons, far above that level of demand. POSCO is one of the major steel suppliers for Japanese automakers in Mexico. Once its new facilities are started, Japanese steel manufacturers would have to secure non-Japanese automakers to which to allocate their capacity.
Despite such conditions, steel manufacturers are making inroads into Mexico. They need to have local processing capability in order to respond to automakers’ requests for an enormous variety of steel materials in a flexible and timely manner. However, upstream processes such as hot strip production require huge investment. Localizing these processes aimed solely at automotive demand is not economically rational. Thus, a realistic choice will probably be to construct galvanizing process lines with an investment of approximately 30 billion yen per line (about 0.4 million tons).
Reality of Localizing Auto Steel Material Supply
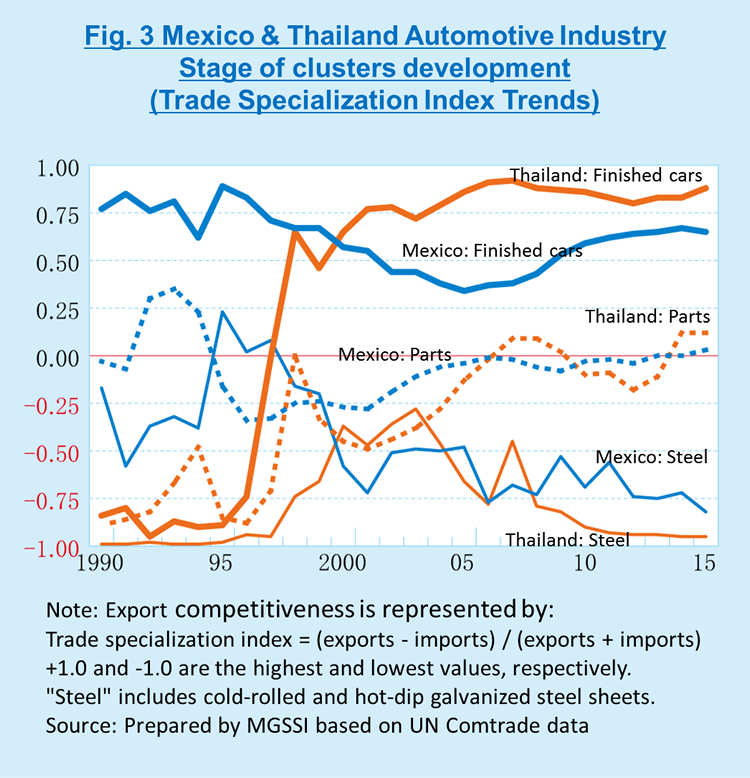
Thailand, the center of Japanese automakers’ production in Southeast Asia, is thought to have clusters of related industries. Nonetheless, when it comes to steel material supply, localization is lagging, too. This fact is clearly shown by the “Index of Trade Specialization,” an indicator of the international competitiveness of a specific product of a country based on its exports and imports in value terms (Fig. 3). In the index, Thailand and Mexico currently have extremely high positive values for finished cars, which implies that both countries have been expanding assembly and export activities. For auto parts, in contrast, the two countries’ values are hovering around zero. This means that auto parts supply is becoming more specialized among the two countries and their respective neighboring countries, which is also activating exports and imports. However, steel materials show a notable decline, inversely with the increasing finished cars and auto parts, and the figures at the current low levels suggest total dependence on imports. Although positioned as a processing and assembly center, both countries have yet to possess sufficient local capability to supply high-quality steel base materials for processing and assembly. Therefore, as more vehicles are assembled, dependence on imports will increase accordingly.
In Thailand, Nippon Steel & Sumitomo Metal and JFE commenced operation of hot-dip galvanizing lines by using imported steel base materials in 2013, much later than the start of assembly operations in the country. Against this background, Thailand and Mexico underwent a different development process than countries such as Japan and Germany, where the basic materials industry rose first, and the machinery and automotive industries ensued, solidifying their respective foundations. In contrast, Thailand and Mexico started as assembly hubs for automakers of developed countries, which was followed by the development of supporting industries. Also in Mexico, the steel industry has a long history, with the establishment of an integrated steel plant in 1900, but its development was initiated by foreign companies, especially those from the US. As a result, the industry suffered capital outflows at the time of several debt crises, which destabilized its business foundation, and thus delayed the modernization of the industry. And the country’s geographical location—adjacent to the US, a giant steel supplier—may have been a constraint on the economic development of Mexico’s steel industry. Moreover, unlike those of other emerging countries, such as India and China, the Mexican and Thai markets are too small, and it is almost impossible to break even on large investments needed for upstream product supply. The market scale may have been a major factor that blocked full localization of steel supply in both countries. Meanwhile, Mexico’s automotive industry is seeing it as a challenge to tackle the delay in localizing supporting industries in its value chains. Thailand, seemingly having advanced industrial clusters, is facing the same problem with steel material supply. These problems can be attributed to the way in which industries have developed in the countries and to a market size that cannot economically rationalize the introduction of an integrated upstream supply chain.