Mitsui & Co. Global Strategic Studies Institute
Challenges and Prospects for Mexico’s Growing Automotive Industry
May 2, 2016
Kosuke Nishino
Industrial Studies Dept. I, Mitsui Global Strategic Studies Institute
Main Contents
With continuing growth in its automotive industry, Mexico produced 3.57 million vehicles in 2015, making it the seventh largest automobile producer in the world. While the automotive industries in emerging countries are suffering slumps, automakers in Mexico, including Japanese affiliates, are expected to expand their production into 2020 on an even greater scale. Isn’t there a blind spot in the automotive industry in Mexico?
Growing Production, Limited Domestic Market
In 2015, Mexico’s automobile output hit a record-high 3,565,000 units, up 5.6% YoY (Fig. 1). Although motor vehicle production in North America plunged in the wake of the collapse of Lehman Brothers, Mexico’s output surged nearly 2.3-fold from 2009 on the road to recovery, while Canada has experienced sluggish production growth.
Automobile output in Mexico has been increasing as the country has become better positioned as a hub to supply automobiles to North America (the NAFTA zone). Due to the financial crisis in late 2000’s , US automakers’ output temporarily fell by half and their production capacity was reduced to two thirds in North America, but most of their capacity cuts occurred in the US. Production in Mexico, conversely, rebounded soon after the drop in 2009. High-ranking Nissan, Volkswagen (VW), and three US companies (GM, Ford, and Chrysler) invested in production upgrades, as planned before the crisis, and in 2014, Mazda and Honda plants commenced operation one after another, which tremendously increased automobile production capacity in Mexico. In addition, there is a series of new plants to be constructed by Kia Motors, Audi, BMW, and Toyota Motor by 2019 (Fig. 2). - Behind this is the fact that wages for workers in Mexico are as low as one sixth or seventh of the US average, where workers protected by powerful union like UAW maintain high wages, thus contributing to lower labor costs in the country’s operations. As a result, Mexico has continued to expand production of automobiles, especially l, low-end, slim-profit small cars.
Mexico has been increasing production on a steady pace, but when it comes to its domestic sales of new cars, the growth has been limited. New car sales in 2015 hit a record-high 1,388,000 units, up 18.8% YoY. Mexico’s new car sales hit one million units for the first time in 2002, and the average annualized growth rate from that year through 2014 was a mere 1.3%.
Behind the minimal growth rate lies the regulation issue pertaining to the import of used cars in Mexico. In accordance with NAFTA’s agreement, Mexico lifted a ban on the import of used cars from the US and Canada in 2005. To protect the sales of used cars distributed in Mexico’s domestic market, only 10 to 15 year-old cars were initially allowed to be imported, but the regulation was gradually eased, and all used cars will eventually become importable by 2019. With the easing of regulation, larger volumes of imported used cars have been brought into Mexico, and now it is said that used cars imported from the US account for 40% of vehicles sold in Mexico, including new cars. The vehicle penetration rate in Mexico is about 30% of its total population, which is not a low rate considering its income level, but due to massive inflows of used cars, the number of new cars sold annually is limited to one thirtieth of the total number of cars owned, which is extremely small compared with other countries. That is a natural consequence, given that Mexico has no tariff or import restrictions in place and is contiguous to the US, whose income level is three times higher than that of Mexico.
North America Centered Export Market Structure, and Fragile Parts Procurement Network
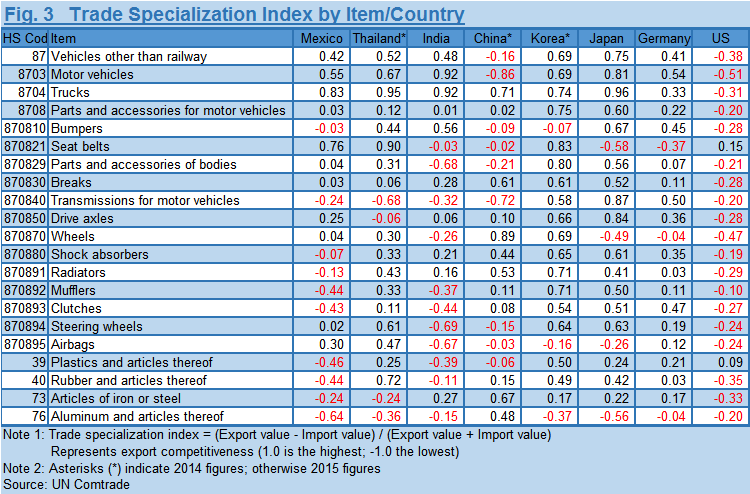
Approximately 80% of automobiles produced in Mexico are exported. 80% of those exports are destined for the other two NAFTA countries, i.e., the US and Canada. While automobile output and exports more than doubled over the past ten years, Mexico’s domestic market had remained at almost the same level up to 2014. Thus, the Mexican automotive industry’s heavy reliance on export to North America has not fundamentally changed.
To facilitate the import and export of automobiles and auto parts, Mexico has concluded economic partnership agreements with 45 countries as export destinations, through NAFTA and also bilateral FTAs with countries in Latin America and the EU, as well as Japan. Under the aegis of Mercosur, a major regional partnership in which Mexico has observer status, Mexico and Brazil concluded an FTA on finished cars. This helped increase Mexico’s exports to Brazil, but at the same time, caused an imbalance in Brazil. As a result, Brazil imposed a restriction on Mexico’s duty-free finished-car exports in 2012, which is still in effect. In addition, Europe-bound exports are limited to certain models of Volkswagen cars. This has prevented exports to other regions from increasing at a desired pace, which is another factor underlying Mexico’s unchanged dependence on the North American markets.
However, in terms of the supply system in Mexico, there has been an increase in production capacity for finished cars, and subsequently parts, since after the financial crisis. The US’s Detroit Three, as well as Volkswagen, are further increasing engine/transmission production capacity. Meanwhile, a spate of new automobile plants established by Japanese automakers have prompted Japanese Tier 1 suppliers to expand their operations to Mexico, and now most major companies have a presence in the Mexican market. By the end of 2015, the number of sites set up by Japanese companies has reached nearly 1,000, reportedly more than doubled over the past five years. Against this background, it has been pointed out that there is a shortage of local suppliers of materials such as aluminum, steel, resin and rubber, primary processed parts like aluminum casting, forgings, pressed parts, and plastic injection moldings (Fig. 3). These are the materials and basic processed products positioned at the foot of industry. This stage is handled by Tier 2 and Tier 3 suppliers from the standpoint of automakers. Each material manufacturer makes such a huge investment in plant and equipment that it cannot be recouped without a certain level of demand. Infrastructure such as power and water are also essential. However, in addition to unstable power supply in Mexico, water supply is limited on the Central Mexican Plateau, where many Japanese companies have flocked to commence operations. Moreover, many of those Tier 2 and subsequent parts manufacturers are small- and medium-sized companies. With limited funds and manpower, it is not easy for them to expand overseas, whether they are Japanese companies or not. Guanajuato, a state where Mazda and Honda plants are located, is essentially poor in industrial infrastructure, and securing manpower of adequate quality is said to be also a challenge for companies that have commenced operations there.
Therefore, Tier 1 parts manufacturers are dependent on imports, such as from the US and Japan, for many of their materials and parts. Currently, even if a manufacturer of finished cars has a local content rate of 70%, the gross local content rate, with all parts and materials included, is likely to be 30% to 40%. In addition to NAFTA, Mexico has FTAs with Japan and the EU, which have helped minimize barriers to importing parts and materials, but also prevented the expansion of local procurement. Moreover, regarding Mexico’s transport infrastructure, such as ports and trucks, transportation costs are relatively high, partly due to an oligopoly of existing operators. Consequently, parts procurement costs are relatively high in Mexico, even when compared with those in Japan and the US. Despite lower labor costs, it may not be easy for new entrants to find a cost advantage in automobile assembling in Mexico. There are some exceptions, such as Nissan’s plants in Aguascalientes and VW’s plant in Puebla. In these areas, with high volumes of production, the accumulation of manpower and related industries over the decades has realized lower-cost operation than in the US.
Prospects and Challenges for Industry Sophistication
How will Mexico’s automotive industry develop in the future? Mexico’s greatest advantage in automobile production is the supply of low-cost factory labor. In the first place, Mexico’s wage level is different from that of the US, and moreover, Mexico’s wage increase rate over the past decade is between 1% and 2%, lower than the US’s, which is between 3% and 4%; thus, the labor cost advantage can be maintained. On the other hand, the supply of engineers and managers, who play a central role in the management of operations in automobile production, is insufficient, and there is merely a 10% difference in salary level for these classifications between Mexico and the US. Although possessing an advantage in the labor-intensive vehicle assembly process, Mexico does not provide cost advantages in the areas such as local procurement of parts and material to increase value-added in the country, or the start-up of new-model production at plants, the design and development of new cars, among others - which are called the brains of the automotive industry -, and not much progress has been made in capacity development, either.
Mexico’s automotive industry has thus far centered on assembling vehicles by taking advantage of cheap labor and sending those finished cars to the US, a large neighboring market. In terms of the entire country, Mexico is experiencing a demographic dividend period, which is anticipated to continue into the mid-2030s, blessed with a large young labor force. Therefore, it is unlikely that labor costs in Mexico will rise. Even if production were to expand in scale, it would be possible for Mexico’s automotive industry to maintain its position as an assembly site for North America, as long as such labor supply continues. However, on the Central Mexican Plateau, which has been tapped by numerous Japanese companies for years, the wage level is expected to increase in association with a surge in labor demand. In the future, if there were a wage increase that exceeded an increase in labor demand, the benefit of automobile production in Mexico might be diluted.
Some parts companies operating in Mexico are manufacturing components in-house for themselves, because not only are imports relatively expensive, but procurement costs are likely to fluctuate along currency exchange rates. In order for Mexico’s automotive industry to continue generating stable revenues for years to come, it should increase local procurement, expand added value domestically, and build a revenue base independent of currency movements. To this end, it is necessary to establish measures to attract foreign companies, such as tax benefits that will help form a cluster of supporting industries, and to develop infrastructure needed to provide an adequate environment for companies to operate.
It is also critical for Mexico’s automotive industry to develop and strengthen capabilities for new model development and related activities such as local procurement of parts. Enhancing the pool of human resources for these core activities of the automotive industry means not only increasing added value but also forming a middle class of possible automobile purchasers, eventually leading to expansion of the domestic automotive market. For Mexico’s automotive industry, this virtuous cycle will also provide a path towards developing independence, instead of being excessively reliant on other countries.